The Importance of 3D Printing Gases: Materials, Safety, and Quality
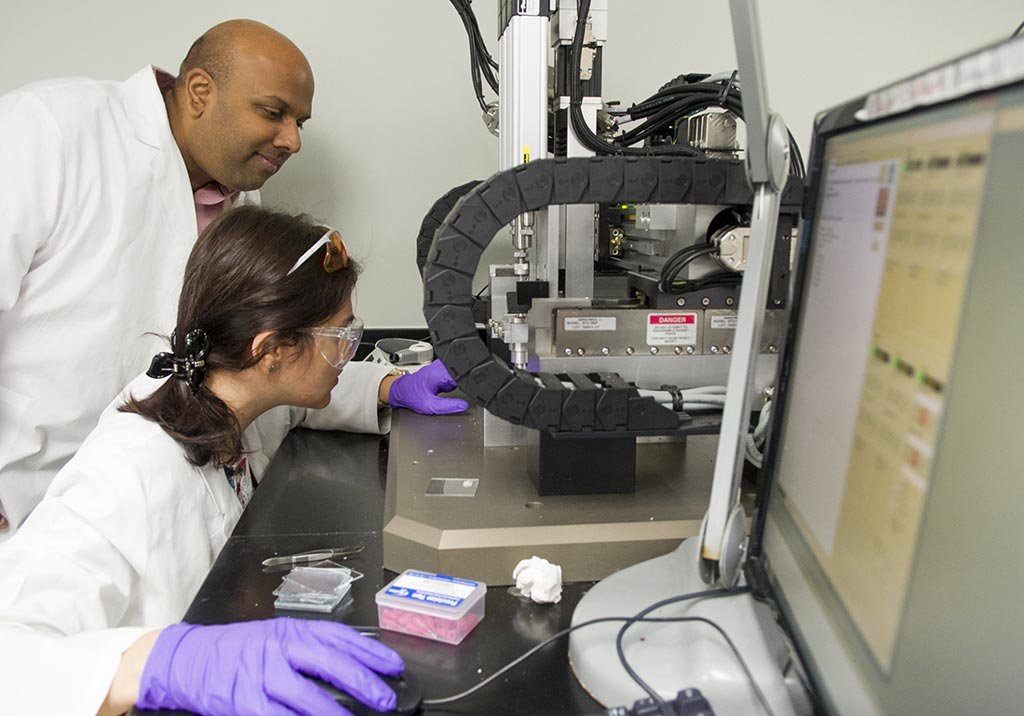
The role of industrial gases in the 3D printing industry is both critical and often underestimated. These gases quietly but effectively contribute to the success of the printing process, impacting materials, safety, and the overall quality of prints. So, this article will explore the practical significance of 3D printing gases in additive manufacturing, focusing on their role in materials preservation, safety enhancement, and print quality.
The Foundations of 3D Printing
3D printing is a revolutionary approach to producing objects. Unlike traditional manufacturing methods that rely on subtracting material to shape an object, 3D printing builds objects layer by layer. This layered approach has opened new doors in industries ranging from aerospace to healthcare.
The Crucial Role of 3D Printing Gases
Within the world of additive manufacturing, gases play a pivotal role in ensuring the success of the printing process. Now, let’s delve into how 3D printing gases are indispensable in three key aspects.
Materials: Preserving Integrity
Controlled Atmosphere for Sensitive Materials: Some materials used in 3D printing are highly sensitive to oxygen and moisture, which can degrade them and affect print quality. 3D printing gases maintain a controlled environment within the printer, protecting these delicate materials from environmental factors.
Temperature Management: Precise temperature control is vital in 3D printing. 3D printing gases help maintain consistent temperatures throughout the process, preventing overheating or cooling that can result in print defects.
Safety: Creating a Secure Environment
Protection Against Hazards: Certain 3D printing processes involve high-energy lasers and heated materials, posing potential safety risks. Gases act as a protective barrier, managing these risks and ensuring a safe working environment for machinery and operators.
Oxygen Reduction for Fire Prevention: 3D printing gases can reduce oxygen levels in the printing chamber, reducing the risk of fires or explosions, especially when working with materials prone to combustion.
Quality: Elevating Precision
Uniform Print Quality: Gas control systems maintain a consistent atmosphere throughout the printing process. This uniformity is crucial for achieving high-quality prints and preventing defects that could compromise the final product.
Enhancing Precision: In 3D printing methods that use lasers or UV light, such as Stereolithography (SLA) and Digital Light Processing (DLP), gases create an optimal environment for the curing process. This enhances the precision of each layer, resulting in impeccable prints.
The Variety of 3D Printing Gases
Different gases serve different roles in the additive manufacturing process, contributing to its success:
Inert Gases: Inert gases, like nitrogen, are often used to create an oxygen-free environment, shielding materials from degradation and maintaining stable print conditions.
Argon: Argon is favored for its effectiveness in preventing oxidation, especially when working with metals.
Carbon Dioxide (CO2): CO2 finds its application in specific laser-based printing techniques, aiding in the curing process and enhancing print quality.
The Continuing Advancements
As technology advances, the role of 3D printing gases continues to evolve. Researchers and engineers are continually exploring innovative ways to refine gas flow control systems, optimize gas blends for specific materials, and enhance overall process monitoring.
Conclusion In summary, 3D printing gases are essential elements in additive manufacturing, ensuring that each layer of the creation is as precise and flawless as the last. Whether it’s the production of intricate prototypes, aerospace components, or essential medical devices, these gases remain indispensable for precision, safety, and the overall quality of 3D prints. They are a testament to human ingenuity, enabling the transformation of innovative ideas into tangible realities, one layer at a time.