Medical PCB Assembly and Manufacturing
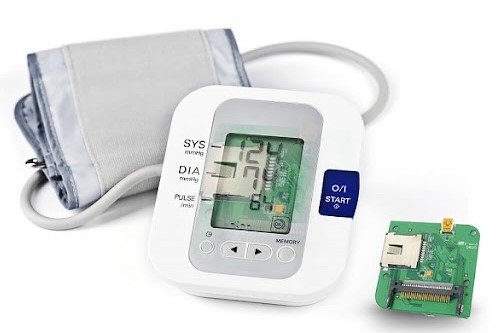

Welcome to the fascinating world of medical pcb assembly and Manufacturing – where cutting-edge technology meets life-saving advancements! In today’s fast-paced healthcare industry, precision and reliability are paramount when it comes to medical devices. Whether it’s a pacemaker, an MRI machine, or a vital signs monitor, every piece of equipment relies on the intricate assembly of Printed Circuit Boards (PCBs) to function seamlessly. Join us as we delve into the depths of this crucial process, exploring the specialized materials and techniques used, as well as the importance of rigorous testing and inspection. So strap in for a journey through innovation and precision that brings us one step closer to improving healthcare outcomes for all!
The Importance of Quality and Reliability in Medical PCB Assembly
Quality and reliability are paramount when it comes to medical PCBs. These electronic components play a crucial role in the functioning of medical devices, ensuring accurate diagnoses and safe treatments for patients. Imagine the consequences if a PCB were to fail during a critical moment in surgery or patient monitoring! That’s why manufacturers must prioritize these aspects throughout the assembly process.
When it comes to medical PCBs, precision is key. Every component must be carefully selected and placed with utmost accuracy to ensure optimal performance. Any deviation from specifications could lead to malfunctioning devices or inaccurate readings, which can have serious implications for patient health.
Reliability is equally important in medical PCBs. They need to function flawlessly under demanding conditions such as temperature variations, humidity, and mechanical stress. Medical devices often operate continuously for extended periods without any room for error. Therefore, manufacturers must rigorously test their assembled PCBs to ensure they meet high-quality standards before they reach healthcare professionals.
Additionally, strict regulatory requirements further emphasize the importance of quality and reliability in medical PCB assembly. Compliance with industry standards such as ISO 13485 ensures that manufacturing processes adhere to specific regulations related to safety and effectiveness.
Maintaining high levels of quality and reliability in medical PCB assembly is essential for patient care and safety. Manufacturers must invest in advanced technologies, stringent testing protocols, trained personnel, and specialized materials—all aimed at delivering top-notch products that healthcare professionals can rely on every day.
The Role of Testing and Inspection in Ensuring Safety and Effectiveness
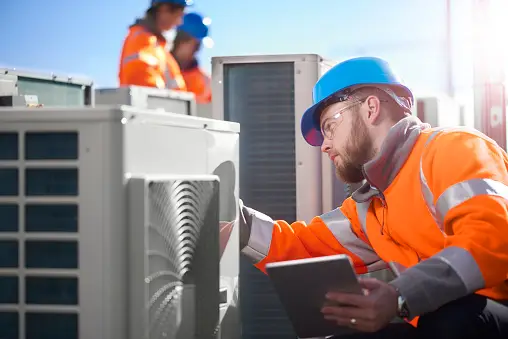
Testing and inspection play a crucial role in ensuring the safety and effectiveness of medical PCBs. These rigorous processes are essential to identify any defects or flaws that could compromise the performance of these critical components.
In the medical field, precision and reliability are paramount. A single malfunctioning PCB can have serious consequences for patients’ lives. Therefore, thorough testing is necessary to validate the functionality and quality of each assembled board.
During testing, various parameters such as electrical performance, thermal management, signal integrity, and mechanical stability are carefully evaluated. Specialized equipment is used to simulate real-world conditions that the PCB may encounter during its lifespan.
Inspection also plays a vital role in maintaining quality standards. It involves visually examining each component on the board for any visual defects like solder bridging or misaligned parts. Automated optical inspection (AOI) systems further enhance this process by detecting minute defects that may not be visible to the human eye.
Additionally, functional testing ensures that all electronic components work together seamlessly when integrated into larger medical devices or equipment. This step verifies if all connections are correct and if communication protocols function correctly.
The ultimate goal of testing and inspection in medical PCB assembly is twofold: guaranteeing patient safety by eliminating potential risks associated with faulty boards while ensuring optimum performance for accurate diagnosis or treatment delivery.
By adhering strictly to these comprehensive procedures, manufacturers can minimize errors in production while meeting stringent regulatory requirements imposed by authorities such as the FDA (Food & Drug Administration).
Common Challenges Faced in Medical PCB Manufacturing
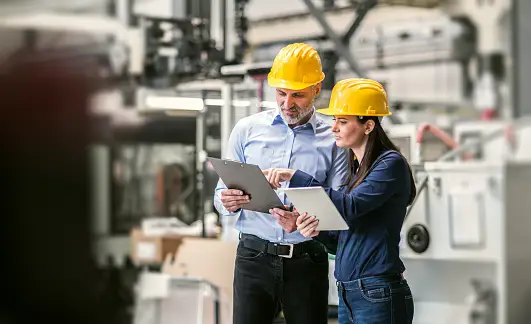
Manufacturing medical printed circuit boards (PCBs) comes with its fair share of challenges. These challenges are unique to the healthcare industry and require specialized knowledge and expertise. Let’s take a closer look at some of the common hurdles faced during medical PCB manufacturing.
One significant challenge is ensuring compliance with stringent regulations and standards. The medical field demands strict adherence to quality control measures, safety guidelines, and regulatory requirements. Manufacturers must navigate through complex documentation processes and maintain meticulous records to ensure that their products meet these rigorous standards.
Another challenge lies in selecting suitable materials for medical PCBs. Medical devices often operate in harsh environments, such as high temperatures or exposure to bodily fluids. Therefore, choosing materials that can withstand these conditions without compromising performance becomes crucial.
Additionally, designing for reliability poses another hurdle. Medical PCBs must be able to function flawlessly over an extended period while maintaining accuracy and precision. Designers need to consider factors like thermal management, signal integrity, and electromagnetic interference (EMI) protection when developing these intricate circuits.
Furthermore, miniaturization presents yet another obstacle in medical PCB manufacturing. With advancements in technology leading towards smaller form factors for medical devices, manufacturers face the challenge of fitting increasingly complex circuitry into ever-shrinking spaces while ensuring optimal functionality.
Supply chain management plays a critical role in overcoming challenges faced during medical PCB manufacturing. Sourcing reliable components from trusted suppliers is essential to guarantee the quality and reliability of the final product.
Future Innovations in the Industry
As technology continues to advance at a rapid pace, the field of medical PCB assembly and manufacturing is also witnessing significant innovations. These developments are aimed at improving the safety, effectiveness, and functionality of medical devices for better patient care.
One area that holds great potential for future innovation is miniaturization. With advancements in microelectronics and nanotechnology, we can expect to see even smaller and more compact medical devices. This will not only enhance portability but also enable more precise and targeted treatments.
Another exciting area of development is wireless communication within medical devices. By incorporating wireless capabilities into PCBs, healthcare professionals will be able to remotely monitor patients’ vital signs or adjust device settings without direct physical contact. This will revolutionize telemedicine and improve access to healthcare in remote areas.
Moreover, personalized medicine is gaining traction as an emerging trend in the medical industry. Customized PCBs can be designed specifically for individual patients based on their unique genetic makeup or health conditions. This customization enables tailored treatment plans that are more effective while minimizing side effects.
Furthermore, there is ongoing research on integrating artificial intelligence (AI) into medical PCBs. AI algorithms can analyze large amounts of data collected by sensors embedded within these boards to provide real-time insights on patient health status or predict potential complications before they arise.
Sustainability is becoming increasingly important in all industries including healthcare. In the future, we can expect to see eco-friendly materials being utilized in PCB assembly processes along with more efficient energy consumption practices.
The future of medical PCB assembly and manufacturing holds immense possibilities for innovation across various aspects such as miniaturization, wireless communication, personalized medicine, integration of AI technologies, and sustainable practices. These advancements have the potential to significantly impact patient care by enhancing device performance while ensuring safety and reliability.
Conclusion
In the fast-paced and ever-evolving field of medical technology, the importance of quality and reliability in PCB assembly cannot be overstated. From intricate surgical instruments to life-saving monitoring devices, medical PCBs play a crucial role in ensuring the safety and effectiveness of healthcare equipment.
With specialized materials and techniques tailored specifically for medical applications, PCB manufacturers are able to meet the stringent requirements set by regulatory bodies. These materials offer enhanced durability, thermal stability, biocompatibility, and resistance to moisture, making them ideal for use in critical medical environments.
Testing and inspection also play a vital role in ensuring that these PCBs meet industry standards. Rigorous testing procedures help identify any potential defects or malfunctions before they are integrated into medical devices. This helps safeguard patient lives and ensures that healthcare professionals can rely on these devices with confidence.
Despite numerous challenges faced during manufacturing – such as miniaturization demands, complex designs, and strict regulations – advancements continue to be made in this field. Innovations like flexible circuits have opened up new possibilities for wearable health technology while reducing space constraints within traditional electronic systems.
As we move forward into the future of medical PCB assembly and manufacturing, it is clear that constant innovation will drive improvements in both performance and functionality. The integration of artificial intelligence (AI), machine learning algorithms, and 3D printing technologies holds immense promise for enhancing efficiency while maintaining high-quality standards.
Medical PCB assembly requires expertise, and precision engineering techniques paired with top-notch materials to ensure reliable operation under critical conditions. By investing in quality control measures throughout production processes along with continuous research & development efforts focused on innovative solutions – we can expect significant advancements ahead! As technology continues evolving at an unprecedented rate so too does our ability to create increasingly sophisticated electronic components designed specifically around unique needs within the medical sector today; keeping patients safe has never been more important than now when innovations abound us daily.